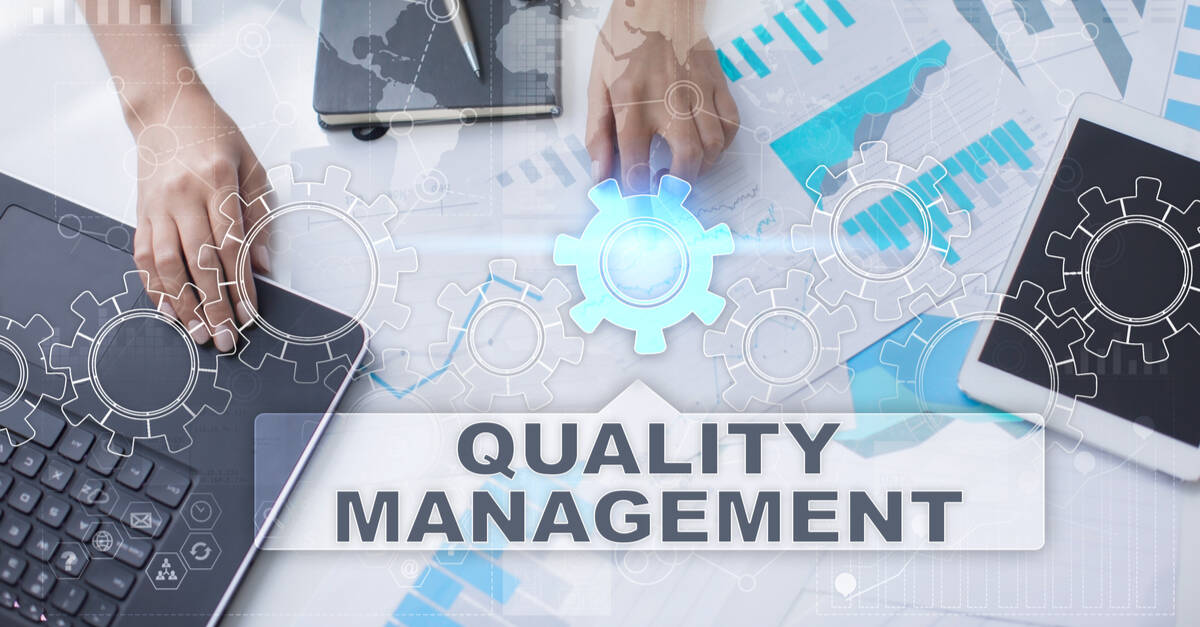
Quality Management: Responsible choosing the correct process to ensure that the product is ‘fit for purpose’.
- A predictable degree of uniformity and dependability at low cost and
- suited to the market (Dr. Edward Deming).
- Degree to which a set of inherit character tics fulfills the requirements
- (ISO-9000)
- Meeting the customer requirements first time and every time which is fit
- for use to its intended functions with reasonable cost and within in time.
- Quality must be measurable and should predictable.
- Quality must be well defined and should be quantified
- Quality objective should be achievable and traceable.
- Quality is Value , Value = Utility (Fit for Purpose) + Warranty (Fit for Use)
- Utility = What customer wants / Warranty = How it is delivered.
- ISO9126 – Quality Standard ( The standard is divided into four parts : Quality model , Internal metrics, External metrics , Quality in use metrics)
Quality Control : “ is the activity performed to ensue that a Product is ‘fit for Purpose’ “.
1. Concentrates on specific products.
2. Defect – detection and correction oriented.
3. Usually done after the product is built.
4. This is usually a line function.
5. Examples : Software testing at various levels.
2. Defect – detection and correction oriented.
3. Usually done after the product is built.
4. This is usually a line function.
5. Examples : Software testing at various levels.
Quality Assurance: “is the activity performed to test the process is being followed”
1. Concentrates on the process of producing the products
2. Defect – prevention oriented
3. Usually done throughout the life cycle.
4. This is usually a staff function.
5. Examples : Reviews and Audits
0 comments:
Post a Comment